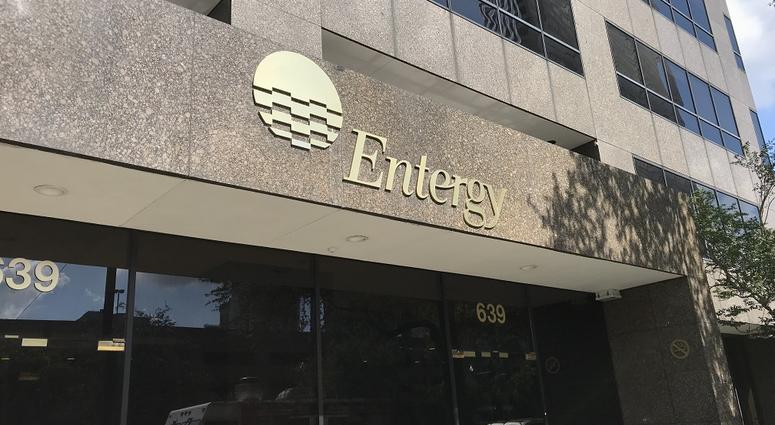
21 Mar The Entergy Case Study
Date of Work: 2006 – 2007
Background:
In the fall of 2006 PBSRG contracted with Entergy Corporation to implement best value procurement into their facilities group capital projects program. Entergy is an integrated energy organization that provides electricity to the Southern United States (Texas, Louisiana, Arkansas, and Mississippi). Due to Hurricane Katrina and increasing energy usage, Entergy desired to increase the efficiency and effectiveness of their facilities capital projects program. This included the delivery and management of construction and renovation of buildings over the southern region of the United States (Mississippi, Arkansas, Texas, and Louisiana).
Perceived issues with PIPS before implementation included:
- Low access and availability to high performing contractors.
- PIPS process thought to be too complicated for local contractors.
Lessons Learned:
- Test projects identified the misperception of clients that high performing contractors are not available in certain areas of the country.
- PIPS process/structure assisted lower performing contractor do performing work. This was validated by returning the contractor to the traditional environment which resulted in nonperforming work, being released from the contract, and Entergy having to hire another contractor to perform the work.
- PIPS dominantly reduced Entergy’s risk management and project management requirements and resulted in higher performance.
- A high performing contractor who normally did not do business with Entergy, agreed to do work under the best value PIPS structure, and performed exceptionally well.
PIPS Performance:
After 9 months of implementation Entergy Facility Management Group was surveyed with the following results (See Tables 15.19 and 15.20):
# | Performance Criteria | Rating |
1 | # of projects (procured/Awarded) | 6 |
1 | # of times Best Value was lowest price | 83% |
2 | Total # of projects completed | 2 |
3 | Customer Satisfaction | 100% |
4 | Change order rate | 0% |
5 | Delay rate | 0% |
Table 15.19: Test Projects Results
- 17% average decrease in project management per project.
- Best Value process was able to select a better performing contractor (100% on time, no contractor generated change orders, and high customer satisfaction.)
- Best Value process forced the contractor to pre-plan, minimize risks that they do not control, create and adhere to a schedule, and to become more accountable.
- Issues were caused more by the client’s representatives and designers.
NO | CRITERIA | UNIT | Previous Process Ratings | Best Value Process Ratings | Difference | |
1 | Measures risk before the project begins | (1-10) | 3.9 | 7.9 | 4.0 | |
2 | Process selects a performing contractor | (1-10) | 5.4 | 8.3 | 2.9 | |
3 | The amount of time spent doing administrative duties for a project | % | 27.50% | 29.83% | 2.33% | |
4 | Documents project performance (amount of risk, cost, schedule, etc.) | (1-10) | 4.7 | 8.2 | 3.5 | |
5 | Minimizes need to manage contractor | (1-10) | 5.0 | 7.4 | 2.4 | |
6 | The amount of pre-planning, risk minimizing, and value added by the vendor, before contract award | (1-10) | 4.3 | 8.1 | 3.8 | |
7 | Requires contractor to minimize risk that they do not control | (1-10) | 3.6 | 8.1 | 4.5 | |
8 | The amount of time required to supervise the contractor | % | 48% | 31% | -17.0% | |
9 | The amount of decision making that is needed on a project | (1-10) | 7.9 | 4.4 | -3.4 | |
10 | Selects contractor that provides most value to Entergy | (1-10) | 4.8 | 8.7 | 3.9 | |
11 | The process documents performance measurements, which create accountability for all parties involved. | (1-10) | 4.9 | 8.4 | 3.5 | |
12 | Requires a schedule at the beginning of projects, assigning accountability. | (1-10) | 6.2 | 8.6 | 2.4 | |
Table 15.20: Entergy Facility Management Group Results (2007)