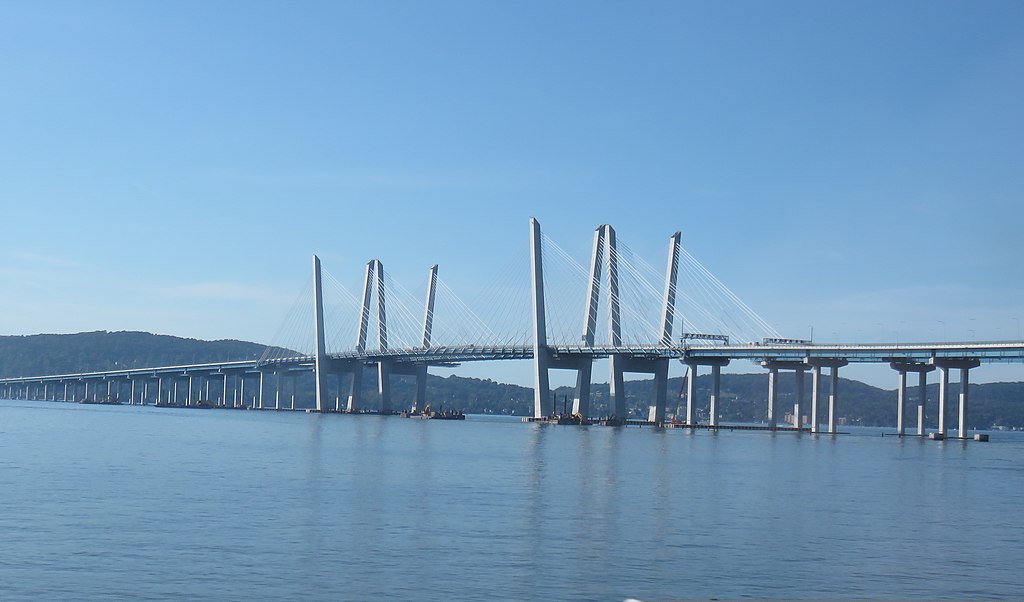
18 Aug Tappan Zee $4B Bridge Project Failure
Legal Disputes on Change Orders
Tappan Zee Constructors (TZC) consisting of Flour, American Bridge, Traylor Bros and Granite Construction, has filed a lawsuit against the New York State Thruway Authority seeking $961 million for extra costs related to:
- Weather delays which occurred at the beginning of the project
- Delays caused by a crane collapse in 2016 which caused TZC to speed up their work
- A third-party engineering firm hired by the State to review and approve decisions made by TZC is claimed to have negatively affected their performance.
What is the Problem?
As large as this project is and its companies, there is no simple plan that is being tracked and no metrics. Without a simple plan from beginning to end and metrics, there is no way to know how much deviation was caused by these issues. For instance, the crane collapsed in 2016—that was five years ago. The weather delays happened even earlier, at the beginning of the project, and the third-party engineering firm had been supervising TZC throughout the project.
Legal issues often occur when there is no transparency in the project. When things are not tracked and measured in a prompt and simple manner, projects become complex. Complexity creates differing opinions and which can lead to more legal actions. When things are simple, legal issues never occur because it is already clear who is at fault. In this project, with the proper plan and metrics TZC should be able clearly show:
- The instances the third-party engineering firm caused performance issues. This could be as simple as showing the expected time for each review period, and the actual time the third-party took to deliver. If the agreed and expected time period was one week and the actual time period was one month, it becomes clear who is at fault and how much time was delayed.
- The weather delays should each be documented by the day, with justification as to why work was not acceptable on that day—this might be because of OSHA standards or weather negatively impacting the performance of the work (rain, wind, or temperature). The client should have been immediately notified for approval. If disapproved, they should be required to give an explanation as to why they disapproved.
- The crane issue is similar in documentation. However, the client should have been notified of the delay and asked to approve the expediting of work for additional funds. If they disapproved, the client would have to accept the delay in days. If the crane collapse was the vendor’s mistake, then this is another issue.
How Can This Be Avoided?
When we use the Best Value Approach, legal issues and disputes on project deviations are never an issue. Before the project starts, the BVA requires a detailed and simple plan which sets the project up for success. The vendor provides this plan, which includes specific things such as:
- Client Action Items and Expectations: This would include a schedule of action items such as approvals needed and an agreed time period which they must be done.
- Assumptions Made by the Vendor: This may include the assumed weather and mitigation plan if assumptions are inaccurate.
- Detailed and Simple Schedules: Together, these schedules should list all the dates and milestones, associated with the cost of the project.
After the client accepts the vendor’s plan, the vendor tracks and measures their performance and deviations which impact time, cost, and quality. The project and potential issues are tracked and reported weekly to the client. When a deviation occurs, the vendor immediately notifies the client with the proper justification documented in the weekly report.
Misperception of Legal Disagreement and Project Issues
This type of weekly reporting has been done on hundreds of projects. The BVA was utilized by the US Army Medical Command on 619 projects, the state of Minnesota on over 399 projects, and the state of Arizona on 195 projects. The biggest misconceptions we dispelled are:
- The project tracking and documentation is to protect the client. In tracking hundreds of projects, we have found the greatest source of risk is always the client. However, the person the client will blame first when deviations occur is the vendor. The tracking and documentation will primarily protect the vendor.
- When deviations occur, and it is documented, the vendor and client will both blame each other and it will lead to litigation. In all the projects we have done there has never been any valid issues or litigation which has occurred. We have learned that most disputes come from poor tracking of time and money. It is only towards the end of the project when time and money run out, that people start tracking the project. It is then that each party, reactively looks to the project’s history to find potential events which they can blame on another party. It is in this process that litigation and legal issues occur.
Conclusion
To avoid legal disputes of project performance of time, cost, and quality a simple plan and method to track a project is required. To learn more about the Best Value Approach and the planning and tracking of projects, here are some resources:
- Free membership for latest tips and news: https://pbsrg.com/membership/
- For latest books, events, and licensed partners: https://pbsrg.com/resources/
- Latest BVA journal publications: www.cibw117.org/
- Annual Best Value Conference in January: https://bestvalueconference.ksm-inc.com/
- Latest presentations and videos: https://www.youtube.com/channel/UCxBi26nXLDTqG4ZRV6p0iiQ